Effects of Lubrication Additive on Contact Fatigue Life of Steel Bearing Rolling Element
Song Baoyu Qu Jianjun Zhang Feng Qi Yulin
(Harbin Institute of Technology, Harbin 150001)
Abstract: Effects of four kinds of lubrication additives on contact fatigue properties of GCr15 chrome steel balls were evaluated on a self-made ball-rod contact fatigue tester. The mechanisms of action of various additives do for steel ball’s contact fatigue were analyzed by means of SEM. The test results showed that 4 of these additives can raise the contact fatigue life of GCr15 steel bearing element to a certain extent. Especially the action of T305 extreme pressure additive and T803 anti-solidifying additive were well.
Keywords: GCr15 Chrome Steel Balls, Contact Fatigue, Lubricant Additive, Ball-rod Contact Fatigue Tester.
The eclipse of fatigue spot is the main of failure mode for the rolling bearing. The research hotspot of scholar at home and abroad is prolong life-span of rolling bearing on contact fatigue. About the influence factor of eclipse of fatigue spot, except for the material and structure of the bearing, One more thing is performance of lubricating oil.
In recent years, home and abroad research focused on how to improve performance of bearing. About performance of lubricating oil, There are fewer studies on that different types of lubricant additive effect on life-span of contact fatigue. Chenming(Chinese name) designed the modified four-ball instrument that is a testing machine of contact fatigue and preliminary investigated effect on a small quantity lubricant acts on contact fatigue. Song-shiyuan(Chinese name) and others have used the test method that contact fatigue of modified four-ball came up by Barwell , In this study, it have 6 different additive effect on contact fatigue. As you see, at present there study about property of lubricant effect on contact fatigue, not only different testing method, but also different additive and mechanism of action. Have not made consensus.
Therefore, the author made use of a self-made ball-rod contact fatigue tester. It has simulated stress condition of bearing. In this study, it has 5 different lubricant additive effect on anti-fatigue performance of rolling bearing material.
1 Test condition
1.1 Principle of testing machine
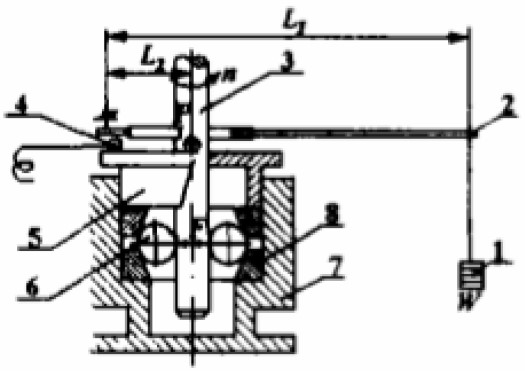
1. loading weights;2. Accelerate lever;3. Steel bar;4. Sensor of accelerate;5. Load case;6. Testing steel-ball;7. bedplate;8. Cone ring
Figure 1 the structure schematic of fatigue tester
Figure 1 is a structure schematic of fatigue tester for ball-rad. The 1 ( loading weights) via 2 ( Accelerate lever ) go through one time of magnify deliver to 5 (Load case). Produce power W, repass 8 ( Cone ring ) make it more. That can be more power between testing steel boll and testing steel bar. Core position of testing in joint between ball and bar, thus 1 ( loading weights ) make two times enlargement get much more contact stress between them.
Sample lubricate is easy. Just need to put lubricating oil in oil tank 7 (bedplate), and get flood the touch point. The smaller oil tank, the less consume of lubricating oil.
1.2 Sample and sample oil
The test uses Փ11mm GCr15 bearing steel bar with roughness Ra=0.4μm and Փ11.113mm GCr15 chrome steel ball with roughness Ra=0.16μm.
In order to study influence of fatigue life-span of rolling bearing on difference addition. We chose 4 different lubricant additives. Weight proportion 1% percent add to machine oil 10# respectively. Number of testing additive and sample oil as shown in the figure (chart1). Sample oil temperature control in 60℃(140F). testing contact stress 6.85Gpa.
Chart1: sample testing addition
classes | EP-Antiwear Agent | Antirusting Agent | pour point reducer | machine oil 10# | |
addition number | T305 | T308 | T747 | T803 | |
sample oil number | T305 | T308 | T747 | T803 | 10# oil |
2 testing results
2.1 parameters of Weibull statistical distribution and distribution
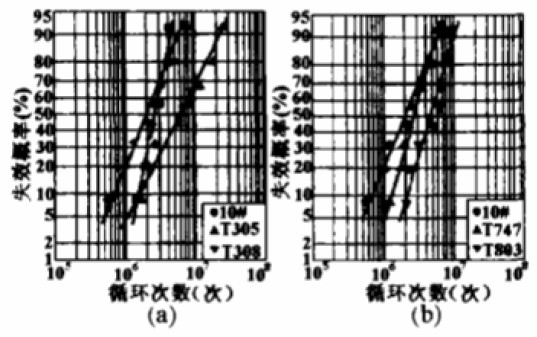
Figure 2 fatigue life span of distribution of Weibull
After acquired the data of fatigue life-span. Then calculate statistic parameter of Weibull distribution. Results are as follow-chart2. From Chart 2 and Figure 2, after comparing with 10# machine oil, some of additives obviously enhance the life span (for instance T305、T803 etc.). but some of them invalidly (for instance T308 etc.)
Chart 2: testing ball-rod statistic parameter of Weibull distribution
Sample oil | Slope of Weibull K | Life-span of characteristic
(105 time) |
L10 life-span
(105 time) |
L50 life-span
(105 time) |
10#oil | 1.2468 | 33.277 | 5.4738 | 24.802 |
T305 | 1.0369 | 103.230 | 11.784 | 72.497 |
T308 | 2.7722 | 31.524 | 14.007 | 27.635 |
T747 | 2.0807 | 33.137 | 11.236 | 27.785 |
T803 | 1.9034 | 60.354 | 18.503 | 49.783 |
2.2 Microgram of fatigue spot
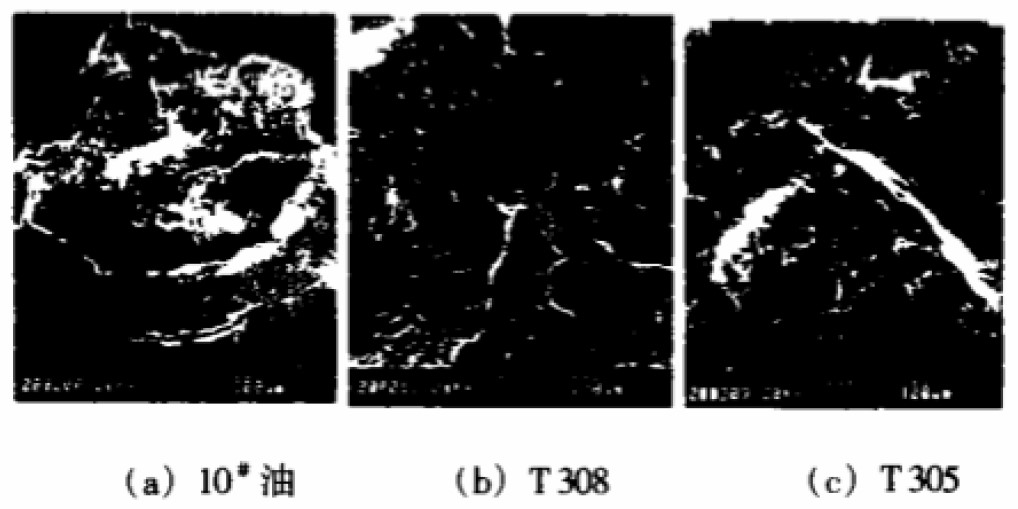
Figure 3 Surface pitting of GCr15 bearing steel ball in microgram
Figure 3 is a microgram (from electron microscope). What can we see on the legend 3(a). the pitting corrosion are scallops likes beans. From the Figure 3 can be informed of there has some scaly or shelly in the scallops. Precisely, crack growth to the figure. The lack of inner material obviously intensity reduce by a large margin in spot of lack. There is easy become source of crack, while cyclic loading working. It will easily produce crack over there. In Figure 3(c) we can see some tiny adsorbate of friction. That shows material shift in the test.
3 Mechanical analysis of addition
Testing results show, by contrast with 10# machine oil, performance of T305(anti-wear reagent at extreme pressure )is better on anti-fatigue. but also T803(contain polar group of pour point reducer), T747(anti-rust agent), T308(anti-wear reagent at extreme pressure).
About the anti-wear reagent at extreme pressure. T305 contain active element of phosphorus sulphur and nitrogen. The other can be come down to phosphorous anti-wear reagent at extreme pressure. There mechanism of action is: under the circumstances of boundary lubrication, friction in the surface, afterwards heat and escape electrons acting on self-catalysis. React with frictional surface. There create organic membrane of contain sulphur or form extreme pressure on iron oxide occasion. Play an important role of anti-fatigue. T308(anti-wear reagent at extreme pressure with phosphorus), There mechanism of action is: take place hydrolysis and pyrolysis film on the frictional surface. Then form reaction film than contain phosphorus compound. Play an anti-fatigue role.
About anti-fatigue mechanism of T803(pour point depressant PPD) and T747(antirust agent). Can be assumed the polar group in molecule are absorbed on surface of friction. Form physical absorption film and chemical reaction film. Reduce direct friction between the surface of steel boll and steel bar. Thereby, enhance fatigue life-span.
4 Conclusion
This text comparative study 10#(machine oil), as well as other 4 different additive lubrication, GCr15 bearing steel ball and GCr15 steel bar rub each other, and measure fatigue life-span. Analysis experiment results. Came to the following conclusions:。
(1) Four different addition, they all can enhance the performance of anti-fatigue. Among them T305(anti-wear reagent at extreme pressure ) and T803(contain polar group of pour point reducer) are better.
(2) electron microscope analysis reveals. From the legend can be informed of there has some scaly or shelly in the scallops. Precisely, crack growth to the figure.
(3) T305 contain active element of phosphorus sulphur and nitrogen. chemical reaction film can working in experience.
T803(contain polar group of pour point reducer). physical absorption film working in experience.
(Translated by Li Xiaole, Luoyang Mingzhen Bearing Steel Ball Co., Ltd.)
References:
[1] 康乃正,毛志远。高应力水平下滚动轴承疲劳寿命试验研究. 材料科学与工程,1996, (9): 45 – 49。
[2] 柴田正道。影响滚动疲劳的各种因素. 国外轴承技术,1996, (2): 32 – 40。
[3] 郑春林,丁锡康,刘晖。滚动轴承的快速疲劳寿命试验及可靠性分析. 轴承,1996, (1): 24 – 28。
[4] 陈铭。润滑油添加剂的复合作用对接触疲劳的影响. 机械设计与研究,2000, (3): 56 – 59。
[5] 宋世远,于江,李子存等。润滑油性能对接触疲劳性能的研究. 润滑与密封,2000, (2): 52 – 53。